This installment from the GeoAmericas Series is timely! The author, Glen W. Toepfer of CQA Solutions, Ltd., will lead an important, free, online discussion on March 27 at 1:00 pm EDT: “COVID-19: Containment System Construction–Foreseeable Problems & Preventive Measures“. Geosynthetica encourages industry stakeholders to join that call. It, like this article, is all about project management and what we can do ahead of and during projects to better anticipate and mitigate disruptions.
INTRODUCTION TO PROJECT MANAGEMENT OF CRITICAL CONTROL POINTS IN GEOSYNTHETIC INSTALLATIONS
The materials, craftsmanship, and technologies are available to produce geomembrane installations that provide superior performance and ROI. For instance, a double-containment geomembrane system comprising over 493-acres of zero-leaks was achieved using such practices and materials, bringing a substantial ROI to the owner (Toepfer et al. 2015).
Likewise, Abigail Gilson (Beck) performed a New York landfill leakage study in 2012, where the Action Leakage Rate (ALR – the leakage rate at which the site is required to take action to remediate the leak) is 20 gallons per acre per day (gpad) and calculated the probabilities of exceeding the ALR under different conditions geared toward geoelectric surveys being performed. The results are summed up in the following statement: “Along with using modern construction methods and a rigorous CQA program, the results of the analysis showed that there is a 22.2 percent probability of exceeding the ALR if no survey is performed, a 7.1 percent probability of exceeding the ALR if only the dipole method is performed and a probability of 0.00001 percent of exceeding the ALR if both the bare geomembrane and dipole methods are performed.”
In order to achieve the type of success listed herein, it is important that the design team understands the geosynthetics with which they are working and the construction process and takes appropriate steps within the design, specifications, and CQA plan that mitigate the risks commonly associated with installations. It is also imperative that the design team understands the owner’s expectations, and properly sets the project up for success through the use of the project specifications and CQA Plan.
2. INVESTMENT
In mainstream construction terminology, geosynthetics are a component incorporated into the project design to serve a specific engineered function, such as containment. From a financial perspective, geosynthetics serve as a valuable asset that can provide a significant Return-on-Investment (ROI) or they can create costly liabilities. In order for an investment to maximize ROI, the investment must be diligently managed.
No matter the size of the project, the initial investment required for obtaining a quality geosynthetics containment installation is significant enough to warrant doing it right the first time. Table 1 shows approximate field and materials costs associated with a standard geomembrane installation.

The costs shown in Table 1 do not include design, certification reports, and other tangible costs that usually are associated with a geosynthetics installation, which all increase the total project cost. Likewise, the costs are broken down to reflect direct times dealing with geomembrane and not installation of other products such as drainage synthetics or cover soils. Additionally, repairs and remediation are tangible short-term and long-term costs associated with improper installation and negative media exposure for such an event is an intangible short and long-term cost that owners do not want to deal with.
In most instances, the owner is afforded little control over the costs shown in Table 1. While the owner can take some efforts to minimize each of the costs through competitive bidding procedures and material selection, there are other, equally important decisions that occur throughout the project timeline that can have as much, or an even greater impact on project ROI. As an owner or project manager, it is important to understand that decisions rendered throughout the project timeline, from conception to construction completion through operational life all impact the ROI.
3. TIMELINE
As an asset manager, it is important to be aware of at least two key phases within the project timeline, which strongly impact the ROI over the life of the project: Design and Permitting, and Procurement of Services.
3.1 Designs and Permitting
Taking time to properly vet and hire the design team that best aligns with the owner’s vision is imperative to starting the project off on the right foot, and ultimately on the track for maximizing ROI. As an owner, you need a design team that is responsive to your requests, as well as one that is not only experienced in geosynthetic design and containment system permitting, but also understands the global view of how construction, installation, and operations all can impact the quality of the installation over the operational life of the system and make or break the ROI expectations of the owner.
RELATED: Dealing with Containment Project Delays – Free Webinar, March 27
The conception and design of the project are typically based on the operational function for which the geosynthetics are intended. In most containment applications, a regulatory agency will govern the permitting and provide guidance into the design elements in order to ensure the design conforms to minimum standards the agency feels are appropriate in protecting the environment from contamination. For instance, many state agencies within the United States limit the amount of liquid that can freely flow out of liquid or wastewater impoundments, which is commonly known as the Allowable Leakage Rate (ALR) or the Action Leakage Rate (ALR). In a 2009 study, it was noted that these rates ranged from 13 gpad (gallons per acre per day) to 6800 gpad (Koerner et al. 2009). In order for a permit to be approved, the engineer is going to have to show that the materials used in the design, when properly installed, will conform to the ALR or other criteria used by the regulatory agency.
It is important for the owner, project manager, and design team to be fully aware of installation materials and products that will yield the greatest chance for the operational facility to conform to the ALR throughout it’s lifetime.
3.1.1 Understanding Geosynthetics Installations.
3.1.1.1 Seam Continuity Versus Seam Integrity; Panel Continuity Versus Panel Integrity
It is important for the designer to understand the relationship between seam continuity and seam integrity. In most instances, seam continuity, such as an air pressure test or vacuum chamber test, is strictly an indicator of whether there are any leaks within the seam being tested. Seam integrity is an indicator of how the seam will perform under in field stresses, and is measured destructively using peel adhesion and shear strength testing of the physical seam. Leak location surveys are primarily a continuity test of the liner that locates holes in the liner. The leak location survey is not an indicator of seam strength, nor an indicator of the true quality of the geomembrane panels themselves.
For instance, using a conductive-backed 60 mil geomembrane as an example, the conductive layer coextruded to the final product is commonly 2-3 mils thick, and always on the bottom side of the geomembrane. This means that you need a damage approximately 57-58 mils deep, or 95-96% of the sheet thickness to expose the conductive layer to in turn activate the detection apparatus. In comparison, the common rule of thumb for assessing which non-penetrating damages to the geomembrane need repair is to repair anything that has incursion of 10% or greater.
3.1.1.2 Destructive Sampling: Minimizing Holes and Maximizing Value
Likewise, the CQA Plan should incorporate a solid destructive sampling plan that serves the purpose of inspecting the production seams, keeping operators honest, and ensuring a high confidence level that seams have been properly constructed while at the same time consciously working to minimize the amount of extra repairs in the geomembrane and allowing the strategic placement of samples such that they can be located away from high stress areas, hard to repair areas, and areas prone to constant liquid exposure, such as sumps. None of these goals are met by a destructive sampling plan whereby the technician marks a sample every 500 lineal feet of weld, without regard to the conditions of the seam and the potential impact of a repair in a high stress/critical area of the system. Additionally, the CQA Plan may allow the flexibility of sampling based on alternative methods proposed by the GRI, such as GM14 Sampling by Attributes or GM20 Sampling by Control Chart.
Similarly, to obtain a superior quality project, seam evaluation turn-around is of the utmost importance because a problem can be identified at an early stage, such as during or after completion of the first seam rather than after the end of a shift, or several shifts and thousands of feet of seam that now need to be repaired. The CQA Plan should address a destructive sampling plan that addresses prompt destructive sampling of completed seams (production and repairs).
One common method that conscientious installers use is cutting end coupons from completed seams and testing them destructively. This method takes little time and at least offers the first opportunity to spot a problem shortly after the seam is completed. Experience has shown that unless the CQA Plan specifies the CQA crew observe the testing of these coupons, the results of such testing may not be accurately reported and serve little value.
Another method, which can reduce the lag time from sampling to results turn-around is the use of an on-site testing laboratory. The on-site testing laboratory can not only reduce shipping costs, but also maximize the feedback available to the engineer, owner, and installer. A competent person evaluating samples in the field laboratory can provide much more detail on the samples and identify trends that lead to failures (for instance, off-center extrusion welds or excessive squeeze-out of thermal fusion welds).
3.1.1.3 Repairs
The CQA Plan should specifically address certain types of repairs that are required in certain instances. For example, an intersection of three or more panels is generally better suited by placing a patch over the intersection rather than a t-bead (thermal extrusion).
3.1.2 Understanding the timeline of Damages
Damages primarily occur in what is called the installation period or in the post-installation period. While there are many factors that impact the amount of leakage through any penetration (ranging from size and shape of the damage, location of the damage both within the containment system as well as whether it is on a flat area in contact with the substrate below, or elevated on a wrinkle, amount of liquid head over the leak, etc.), the goal should be to prevent damages and to locate them if/when they do occur.
3.1.2.1 Installation Damages
For an installation performed with a competent installer with a rigorous Quality Control and competent CQA observation, numerous studies have shown that the amount of holes contributing to leaks will be greatly reduced. That being said, these historical studies have categorized the source of leaks resulting from: tears, cuts, punctures, and seams. The percentages of these vary depending upon various conditions, such as the material type and thickness, the quality and firmness of the substrate (subgrade) upon which the geomembrane is deployed, and the workmanship of the installer. While the design team cannot directly control the workmanship of the installer nor the incidental damages occurring during installation, they can address the materials and specify sound substrates upon which the materials will be placed.
Likewise, the design team needs to understand the difference in seaming methods and the relative implications to quality. Repairs are often performed with an inferior welding technique when compared to the primary method used to join primary seams. For instance, primary seams of PVC, HDPE, and LLDPE are predominately welded using thermal fusion welding methods, while the repairs of PVC are limited to chemical or solvent welding and the repairs of Polyethylene are performed with thermal extrusion fillet welds, both of which are inferior to thermal fusion welding because of their heavy dependence on operator skill. Designing and writing specifications to reduce the amount of repairs required, as part of the installation process, is another way to minimize the number of potential leaks.
The amount and location of leaks can vary from this significantly if the installation is performed with careless installers or even competent installers with the lack of Quality Control and/or CQA presence.
3.1.2.2 Post-Installation Damages
There have been several studies that show a significant portion of damage, especially pertaining to size of holes contributing to leaks, occurs in the post-installation phase of construction when the geomembrane is being covered, and data seems to support the idea that the amount of these damages decreases with the presence of competent CQA.
Likewise, the author has been personally involved in instances where damages occurred to geomembrane systems after the installation was complete and the facility permitted and operational. These damages occurred due to the significant delay between completion and eventual usage during operations. For instance, on one site, several acres of geomembrane were covered with drainage aggregate during the construction but sat untouched by the operational phase (covered with waste) for several months. During the several months, a rain event washed caused significant erosion on the slope, which subsequently allowed deer hooves to penetrate the geomembrane. If not for an observant operator performing backfilling operations, these damages may have gone unnoticed and lead to significant problems in the future.
With the understanding that the post-installation timeline is just as critical, or even more critical than the initial installation, a small bit of insurance, such as requiring full-time CQA coverage during cover placement, designs that incorporate and specify leak location surveys be performed, and periodic, post-installation inspections throughout the operational lifespan of the containment unit can go a long way towards protecting the owner’s ROI.
3.1.3 Design Considerations
3.1.3.1 Material Selection
Obviously, the material chosen for the design plays a huge part in the success of the project maintaining conformance within the ALR over the lifetime of the project. Material selection is based on a number of features such as resistance to anticipated chemicals, resistance to heat, friction requirements, etc.
With the knowledge that leaks are more prevalent on inferior weld types, it is imperative that the design team takes measures to minimize the amount of inferior welds on a project. One method is for the design team to work with manufacturers and design the project shape and boundaries around existing materials or see if the manufacturer can provide custom size geomembrane rolls or sheets – the goal of both being to minimize the number of intersections where repairs will need to be performed. Another consideration should include the width of the material, as wider products can reduce the amount of intersections on some projects, thereby reducing the amount of repairs required.
To maximize the ability to detect leaks, either during the installation period, or post-installation after cover soils are placed, the design should consider the requirements for such methods. For instance, a conductive backed geomembrane will allow for both spark testing during installation, and leak location surveys performed after the geomembrane is covered. Similar abilities can be obtained without conductive backed materials, provided the materials are properly designed and installed.
3.1.3.2 Constructability
Another common weak part of the system in terms of being an area where leaks develop is penetrations through the geomembrane, such as liquid collection pipes, gas vents, etc. which are hard to weld, or may not even have adequate room to perform a competent weld due to a poorly conceived design. Figure 1 shows the extruder being held at an angle to perform the weld – such angles produce difficulty in obtaining a proper grind prior to the extrusion weld, as well as a poor pressure during the welding.
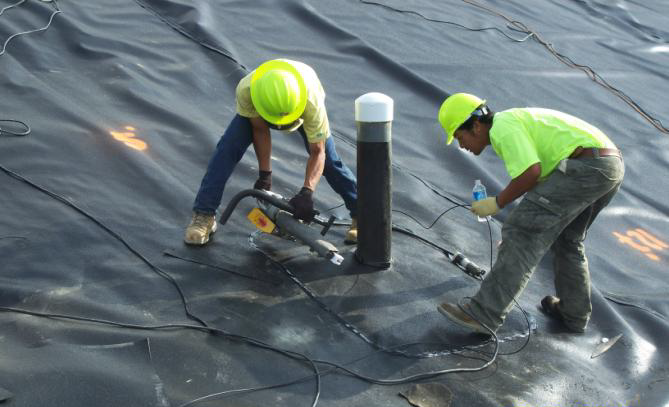
Again, each penetration is going to require an inferior weld type to join it to the geomembrane system. Owners should ensure their design team takes advantage of the wide range of products currently on the market, such as prefabricated boots, which significantly reduces the amount of inferior seaming and generally provides a more suitable edge for joining to the geomembrane, resulting in a better weld quality.
Even the superiority of welding methods such as thermal fusion can be negated if the design or specifications do not allow for proper constructability with the equipment.
3.1.3.3 Modern Technologies
Technology has come a long way since the inception of geosynthetics use as a containment tool. Materials and methods have improved considerably. It is important for the design team to incorporate modern technologies as part of their project. Some of these products can yield significant ROI.
For instance, as mentioned earlier, many studies have also shown that post-installation damage (such as the placement of a cover or drainage layer) contributes to a large percentage of holes in the geomembrane, especially in the absence of competent CQA (Forget et al. 2005). However, the incorporation of leak detection methods or surveys into permitted projects remains relatively low at less than 25% of containment system installations.
3.1.4 Construction Requirements
As the design firm goes through the process, the result will be to develop project specifications and the CQA Plan, which will be the foundational documents upon which all construction is carried out. Ensuring the specifications meet the goals of the owner will in turn help ensure the project ROI is maintained. At the point the design is being performed and the specifications are being developed, it is little cost to add in requirements that bear a huge weight on the quality of the installation and in turn, the project ROI.
The design team should use all resources available in determining the specifications and developing CQA Plan. There are plenty of resources readily available to assist the design team in this function, such as manufacturer’s websites which contain drop in specifications, product installation manuals, application sheets, etc. that can be obtained on the internet and/or through a phone call. Likewise, many installation firms employ engineers that usually are happy to assist in answering questions about designs. The Geosynthetic Institute (GSI) is an excellent resource as well.
3.1.4.1 Project Specifications
It is important for the design team to stay current on project specifications. While it may be easy and tempting to “cut and paste” specifications from one project to another, doing so can be harmful to the project in a number of ways. Over-specifying products to the point it is hard to find a material that works, under-specifying products such that they may be inferior for the design intent, and specifying installation practices that are archaic and compromise quality during installation. Likewise, the specifications should clearly identify methods that will be implemented to reduce the likelihood of leaks, whether a bare geomembrane survey such as a spark test be performed, a dipole survey upon completion of the cover material, or both.
3.1.4.2 CQA Plan
Like the construction specifications, the CQA Plan needs to remain current and practical, otherwise it limits the abilities of the CQA team, potentially limits the abilities of the installer, and may do more harm than good. It is important to empower the CQA team so they can properly perform their function, both in the field and behind the scenes in the office. While many CQA Plan’s do well at focusing on values and procedures of field-testing during installation, there are several common areas that can use improvement.
For instance, the CQA Plan should force the CQA team to competently evaluate material MQA/CQA test results. As an example, a material may meet average tensile strength requirements, but a close examination could show that the average was carried by several high values outweighing some extremely low outliers, which could cause installation or long-term problems when the material is put under stress in the field (Toepfer 2015). It is important that the results be evaluated with the operational functionality of the material in mind and not just a crosscheck of whether minimum and/or average values are obtained.
3.1.4.3 Experience and Education Requirements
The project specifications and CQA Plan are good places to spell out the specific expectations of the construction team members, from education, to relative experience on similar projects, to industry certifications.
3.2 Procurement of Services
There are plenty of variations in the both the qualifications of individual contractors, from the design firm through the construction teams. In order to achieve the highest ROI possible, it is important to determine exactly what you are going to get for your investment. One of the first decisions that need to be made is whether or not to use a turnkey solution for the entire project, whereby one entity is hired to manage the entire project, from design through construction. There are advantages and disadvantages to both, so the decision should not be taken lightly. Regardless of which decision is made, key components of the team should be evaluated.
3.2.1 Design Team
It is important to properly vet the design team to ensure they are capable of designing facilities to conform to the needs of the owner. This may require fully investigating references, asking for samples of similar designs and specifications with similar products on similar projects. Some of the key components to be looking for in a design firm have already been mentioned in this paper.
3.2.2 Installation Team
Choosing a competent installer is one key to obtaining a good final product. Not only should the installation firm be properly vetted by checking out references for projects of similar materials, the proposed crew should also be properly vetted. Not every installer, nor every crew working for one firm, is created equal. “Average hole size and frequency contributing to leakage depends heavily on the skill of the liner installer and the skill of the CQA agency”. [Beck, 2012]
Having a competent installer should result in minimizing the amount of seams, quality seams, and reducing the amount of peripheral damages that occur during the installation process. A competent installer should also be able to adhere to an approved panel layout drawing.
It is important that the installer provide a panel layout drawing for the project, prior to their mobilization on the project. This submittal will allow parties such as the design engineer, certifying engineer, owner, and CQA team to evaluate the plan and determine potential ways to minimize repairs, as well as ensuring constructability of the project.
3.2.3 CQA Team
The CQA team should be thought of as your insurance policy. The role of CQA is particularly important as these field personnel are truly the “eyes and ears” of the project and their ability to not only recognize problems, but bring them to the attention of appropriate parties before things spiral out-of-control is of the utmost importance.
The concept of competent CQA being an insurance policy can be illustrated by one of many studies: According Forget et al. (2005), geomembrane leakage rates go from averaging only 4 leaks per hectare (2.47 acres) with rigorous CQA to averaging 22 leaks per hectare (2.47 acres) without CQA. The presence of competent CQA was the sole contributor that resulted in a substantial reduction in leaks.
Like other subcontractors, the CQA team needs to be properly vetted. CQA personnel should be attentive to the project and work pro-actively with the installer in ensuring the goals of the owner are being achieved. It is also important to understand that CQA is an asset that cannot be replaced by leak location surveys, as has been done on certain projects.
4. CONSTRUCTION
4.1 Contract Structure
There are various contract structures available, and each one has it’s own unique set of dynamics that can impact the ROI of the project. Turnkey solutions typically provide one contractor who manages the entire project, and subcontracts out the work areas in which they do not specialize. Understanding how the turnkey firm vets the subcontractors can go a long way in providing the quality you desire.
Likewise, many projects involve both an earthwork contractor and a geomembrane installer as part of the construction team. In some instances, these entities may be both contracted directly to the owner, thus giving the owner greater control over the project, but also requiring more direct involvement from the owner in terms of managing the separate entities.
A common contract structure designed to minimize owner involvement, especially in the area of being a referee between the parties, is to make either the earthwork contractor or the installation contractor the general contractor and have the other work subcontracted out to the general contractor. Either of these are viable options, but they also both produce their own set of unique challenges, especially when one of the firms does not understand the true importance of the other firm, or becomes bottom line focused which often leads to cutting corners or pushing subcontractors to the point their work quality is jeopardized.
4.2 Material Procurement
More than one project has been delayed, either due to the manufacturing timeline of the geosynthetics, or because of a material shortage during the installation. These delays can be costly, both in terms of hard costs, but also in terms of installation quality.
The procurement process should be started well in advance of the project, and constant feedback should be given on material inventories throughout the course of the project, starting with ensuring the proper amount was delivered to the site prior to the start of the project.
4.3 Pre-Construction Meetings and Progress Meetings
Pre-construction meetings should be mandatory and should include key players from all the represented contractors, including the field personnel performing the installation oversight and QC and the third party CQA field crew leader. Pre-construction meetings are a time where specific details can be ironed out, and differences resolved, before the crews ever hit the ground. An effective pre-construction meeting will yield a significant ROI by giving each party a clear understanding of expectations, methods to resolve differences, and kicking the project off with everyone on the same page.
Larger projects also benefit from regularly scheduled progress meetings, whether weekly or bi-weekly. Having regular meetings allows for regular updates on progress, as well as the opportunity to address hurdles or issues before they snowball into something that starts to compromise quality throughout the project.
4.4 Site Owner Inspections
One way to ensure accountability and instill seriousness about meeting the owner’s objectives is for the owner to periodically visit the site. Site visits allow the owner to see the progress first hand, talk with the different firms, and maintain their finger on the pulse of the project construction. Time is a precious commodity which is all part of the asset management mentality.
4.5 Weather Event Planning
Even with today’s technology and the ability to forecast weather, there simply are times the prognosticators get the forecast wrong, or Mother Nature decides to chart her own course. Weather event planning can go a long way toward mitigating damages that otherwise would have been caused from a lack of preparedness. There are many stories, and even own personal experiences of the author that cannot overemphasize the importance of being prepared for weather events, and how that preparation can pay huge dividends when an event hits your project.
5. R.O.I.
Most battles are won and lost in the “War Room” before the troops ever hit the field. Containment Construction is no different. Containment designs and specifications need to be based on a fundamental understanding of field operations and processes. This ensures a better quality project that can be constructed within a shorter timeline while meeting all regulatory requirements.
5.1 Your Project, Earn it!
A good return on investment requires a lot of attention to detail. It don’t just happen, it is earned. Anything can look like it works on paper, but in order to execute a project properly; it has to be implemented correctly from inception through final
operations with a deep understanding of how plans, specs and construction actually occur in the field. To do this consistently takes leadership with a highly specialized skill set and experience in this niche market.
5.2 Pay for Needs, Not Fluff (cert report, documentation versus observation, electronic)
In asset acquisition, it is important to carefully evaluate what the money is being spent on. The mentality that the leaner the budget, the more return will be yielded is often not the case. However, acquiring all the bells and whistles may not provide any difference in end result in ROI – you may just end up with a bad purchase, such as spending extra money on certification reports, or paying for documentation instead of getting true observation and CQA performance.
As part of the design process, it is important to run a cost benefit analysis and determine your individual tolerance for risk versus reward. For instance, Table 2 gives an example of costs associated with installing a 60-mil HDPE textured geomembrane, as well as additional options. You can clearly see that products and services used or designed to reduce the likelihood of potential leaks will add an additional cost. Is this cost substantial enough to prevent you from incorporating it into your design?

5.3 Data Management (Management by Data)
There are two sides to data management: historical trends, and current trends. In this case, historical trends refer to the industry, and using data sets from the industry (similar to references used in this paper which are published data sets) in your Cost-Benefit Analysis. Sometimes historical numbers are staggering: for instance, one containment project, a 6.5 acre irrigation pond for a golf course/hotel development had a failure cost of $1,300,000 USD due to poor installation and a lack of CQA; a failure of geosynthetic liners used in anaerobic digesters of a wastewater treatment facility cost in excess of $21,000,000 due to poor design, poor installation, and poor CQA, whereas the cost of prevention was $13,000 USD and $40,000 USD respectively.
Current trends refer to data acquired during the current project construction, and using that data to effectively manage the project throughout the construction phase. For instance, a trend may be observed to where seam destructive sample failure rates are higher on days preceding time-off, or at the end of long weeks. In the short-term through the continued duration of construction, steps can be taken to help minimize these failures as well as mandating increased sampling during these shifts. Using such data learned on one project should then transfer over to future projects, which can even be done by modifying the specifications and/or CQA Plan to specifically address these issues.
Having data readily available in real time and a competent person managing and mining the data is another key to increasing ROI.
5.4 Enforce Bid Purchase Request
The ownership mentality is critical to managing a project to maximize ROI. Care must be used not to fall into the mentality of putting all the responsibility on the contractor and allowing them to take over running the project – this mentality puts control of your ROI in the hands of others.
Effective management of the contractor can be done through the bidding process, by setting clear expectations that the contractor is going to be held to. The bidding process and ultimate contract should empower the ROI manager to remind the contractor that these are the conditions that you bid to and what you need to provide. After all, the contractor’s ROI is not tied to the long-term performance of your project. As someone in the mining industry once put it: “It is not the contractor’s gold leaking out of the heap leach containment.”
6. CONCLUSION
Viewing a geosynthetics project as an asset obtained through an initial investment with the goal of maximizing ROI means the owner is fully vested in their investment. As such, there is nothing wrong with the owner setting lofty expectations. In order to achieve these expectations, the owner will need to manage the project in a manner where they maximize control the outcome. As illustrated in this paper, there are many opportunities for management throughout the course of the project and it’s operational life. By setting clear expectations at the conception of the project and managing the project at pivotal control points throughout the timeline, the owner can help chart the course for success and experience substantial ROI.
Being fully vested may mean the project is managed differently, where everything is scrutinized and where can they control the outcome of the project.
REFERENCES
Beck, Abigail, (2012). “How Much Does my Landfill Liner Leak?”, WasteAdvantage Magazine, December Issue.
Forget, Benoit, (2005). “Lessons Learned from 10 Years of Leak Detection Surveys on Geomembranes”, Sardina Symposium, Sardina, Italy.
Koerner, R. M. and Koerner, J. R. (2009). GRI White Paper #15, “Survey of US State Regulations on Allowable Leakage Rates in Liquid Impoundments and Wastewater Ponds,” Geosynthetic Institute, Folsom, PA, USA.
Peggs, Ian and Peggs, Elizabeth, (2005). “Geosynthetics Risk Management and Loss Control Program”, White Paper.
Toepfer, G.W. and Pittalwala, S. (2015). Covering Your Assets – Construction Quality Assurance, Geosynthetics ‘15, IFAI, Portland, OR, USA.
Toepfer, G.W. (2015). The Complete Field Guide To Ensuring Quality Geosynthetics Installations, Volume 1: Fundamentals & Geomembrane. Integrity Matters, Toledo, OH, USA.